𝗣𝗮𝗽𝗲𝗿 𝗪𝗶𝗻𝗱𝗲𝗿 / 𝗥𝗲𝘄𝗶𝗻𝗱𝗲𝗿 𝗥𝗲𝘁𝗿𝗼𝗳𝗶𝘁.
What data required to total upgrade or install new control / drive system of Paper Winder?
𝗣𝗮𝗽𝗲𝗿 𝗪𝗶𝗻𝗱𝗲𝗿 is used to rewind and slit the paper from big jumbo or parent roll to the smaller Roll for shipping.
Tension is maintained steady during running, accelleration and deceleration.
Two drum winder system has Unwind, Front Drum and Rear Drum as main component, and usually driven by DC Drive or AC Drive with regenerative bus supply. Additional drive could be for rider roll, lead in roll and slitter.
Front drum and Rear drum has split torque setting to make sure uniform hardness.
Slippage, strip break, defect roll commonly happen when this system don’t have proper control and tuned properly.
When control/ drive system will be total upgraded, the minimum data that need to be collected are:
* List of motor with nameplate data of all motor.
* List of existing drive if there is.
* Maximum diameter of Parent Roll/ Jumbo Roll.
* Minimum diameter of Parent Roll / Jumbo Roll
* Maximum Tension.
* Paper/ Trim Width.
* Paper gramature in GSM.
* Diameter of Front Drum/ Rear Drum.
* Minimum deceleration time (normally 60 second)
* Emergency stop time (normally 30 second).
* Maximum Speed.
* Gear box ratio data, if use gearbox.
* Roll Diameter for additional roll that driven by drive.
If the schematic diagram is not supplied this additional data is required:
* Total digital input/ output.
* Total analog input / output.
* Total Direct Online (DOL) starter.
* Total remote I/O and distribution of I/O for each remote I/O.
The above data required to properly size and determine the motor, drive, DC Bus supply, and other parts of new control/ drive system.
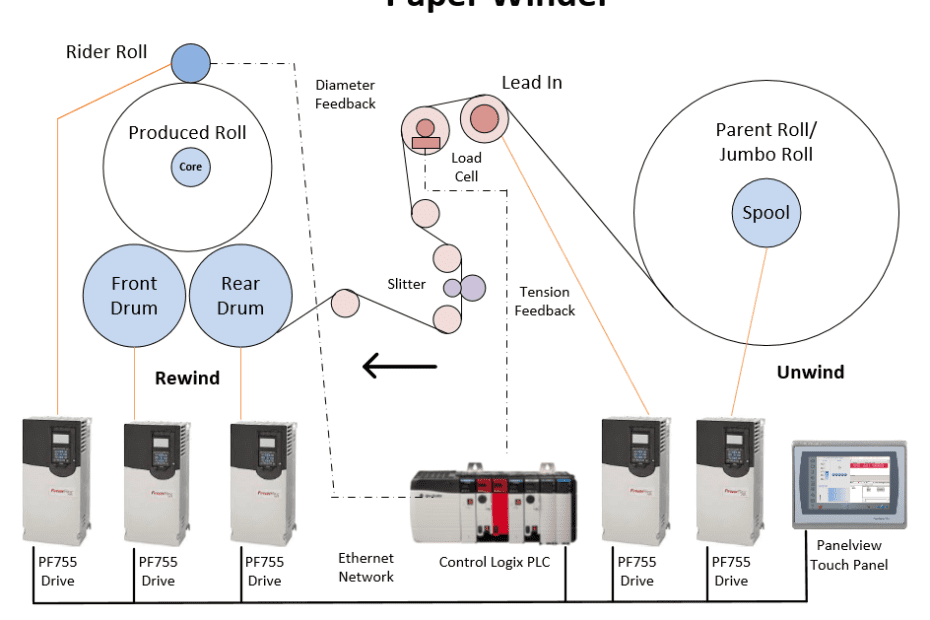