𝗪𝗿𝗮𝗽𝗽𝗶𝗻𝗴 𝗠𝗮𝗰𝗵𝗶𝗻𝗲 – For Soap, Food etc
What can be done to optimize the performance and availability of wrapping machine motion system?
𝗪𝗿𝗮𝗽𝗽𝗶𝗻𝗴 𝗠𝗮𝗰𝗵𝗶𝗻𝗲 is used to wrap the product with paper or film at high speed and precision.
The position of paper/ film to the product and cutting length should be maitained same with high accuracy all the time during running.
Wrapping machine usually has the component as below:
– Paper or film feed roll. Used to feed the paper/ film.
– Cutter /knife to cut paper every certain length or crimper /sealer to seal/ cut film.
– Eye Mark sensor to detect marker on paper which detect position of the paper.
– Product detection sensor.
– Master Encoder. Used to synchronize the paper and cutter position to the product conveyor.
𝗛𝗲𝗿𝗲 𝗮𝗿𝗲 𝘁𝗵𝗲 𝘁𝗵𝗶𝗻𝗴𝘀 𝘁𝗵𝗮𝘁 𝗰𝗮𝗻 𝗰𝗮𝘂𝘀𝗲 𝘁𝗵𝗲 𝗺𝗮𝗰𝗵𝗶𝗻𝗲 𝗻𝗼𝘁 𝘄𝗼𝗿𝗸𝗶𝗻𝗴 𝗶𝗻 𝗼𝗽𝘁𝗶𝗺𝘂𝗺 𝗽𝗲𝗿𝗳𝗼𝗿𝗺𝗮𝗻𝗰𝗲 𝗮𝗻𝗱 𝗵𝗮𝘃𝗲 𝗿𝗲𝗱𝘂𝗰𝗲𝗱 𝗿𝘂𝗻𝗻𝗶𝗻𝗴 𝘁𝗶𝗺𝗲:
1. Paper/ film position is unstable or oscillating when run at high speed ;
– Paper roll tension is too high .
– Higher slippage on the paper/ film feed roll when automatic position correction is enabled. The servo control or programming may not suitable.
– Paper/ film feed roll can not grip paper properly.
– Marker detection can not keep up with the speed of machine. It may due to slow eye mark sensor or motion control signal detection not fast enough.
2. Paper / film not cut at exactly same length when run at high speed;
– Cutter can not keep up with machine speed. Fix or upgrade the servo control.
– Inertia missmatch between cutter motor and load.
– Cutter gearbox have big gear teeth clearance or backlash.
– The cutter motor coupling may not rigid enough, lenght is too long or diameter is too small.
3. Coupling or gear need to be replaced often and motor is hotter than normal;
– Gearbox have big teeth clearance or backlash.
– Motion control not properly programmed or tuned .
4. Product not wrapped correctly during acceleration or when the product not feed continuously;
– Paper or fim is jerking excessively when start and stop. Motion control or programming that implemented may not suitable .
– Wrong product detection sensor placement or setup.
– Paper or film is jumping around when start and stop. Tension stabilizer may not working properly or motor move jerkingly.
5. When having a problem, motion controller not easy to troubleshoot and cause a long machine stop;
– Servo control program can not be accessed for troubleshooting. Replace with user friendly servo control/ drive.
– Servo control already obsolete, no spare part and support available. Replace with the latest servo control/ drive before machine breakdown and not able to run anymore, as engineering and ordering could take more than a month.
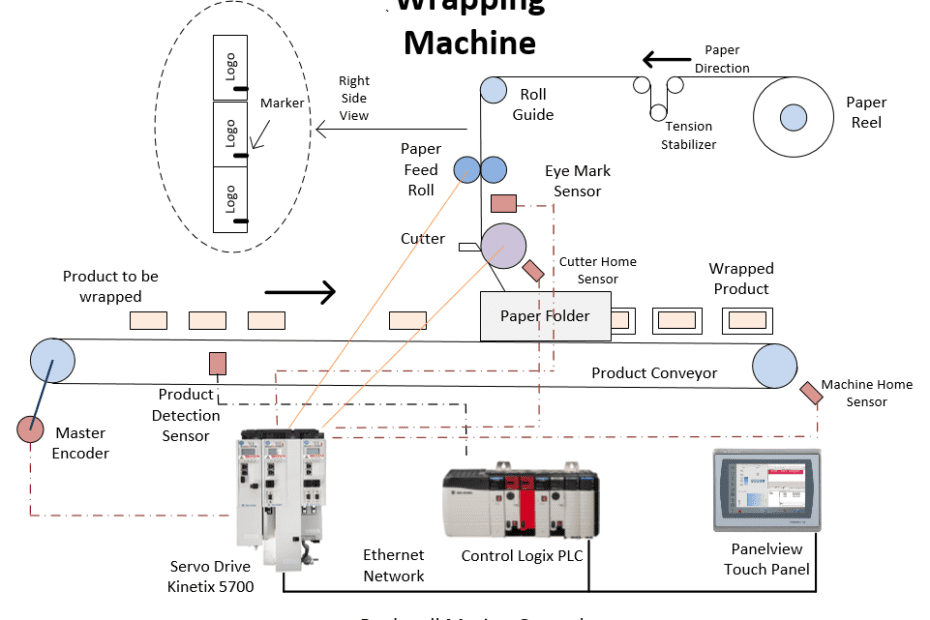